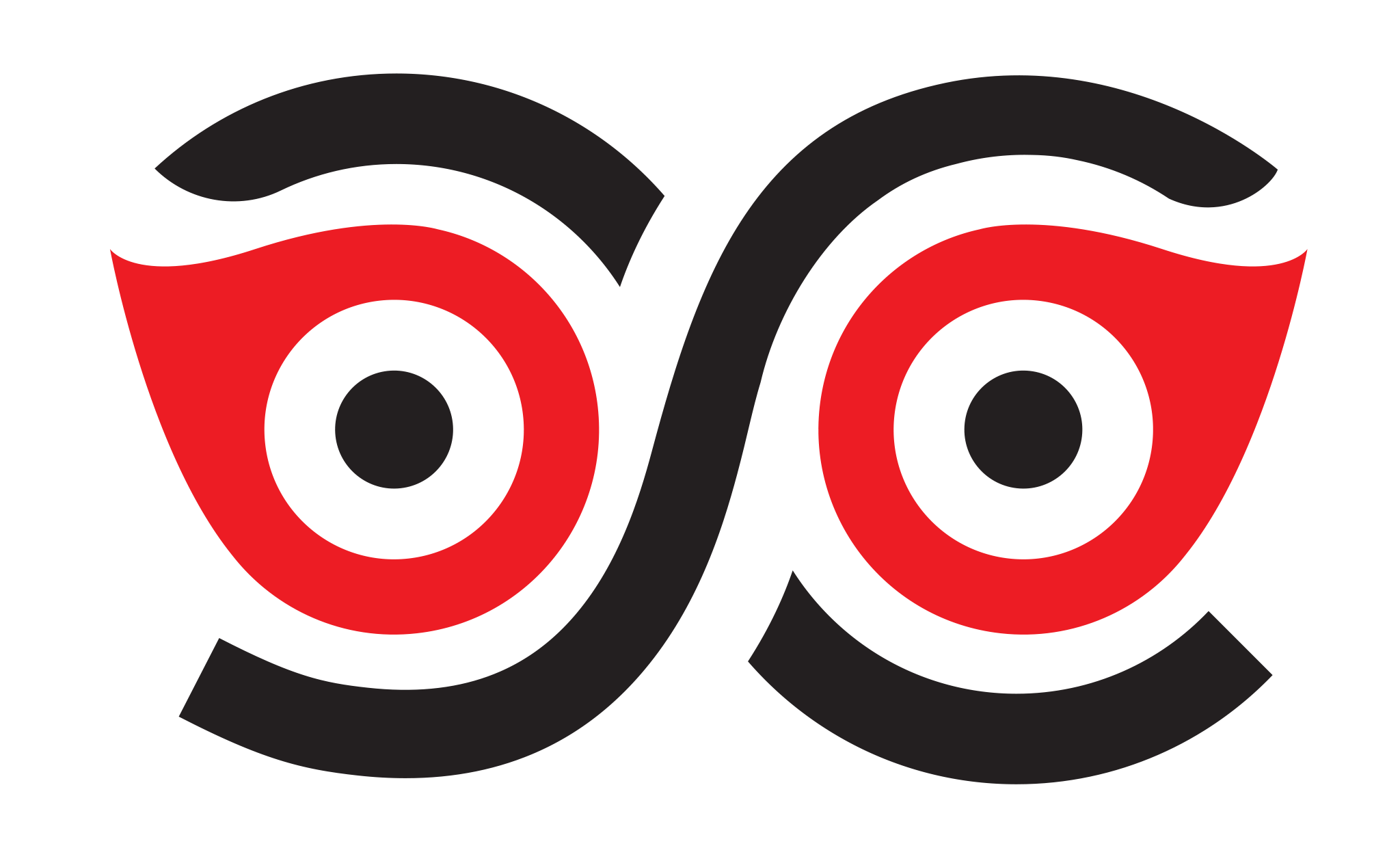


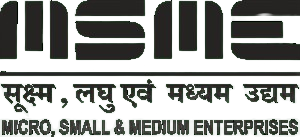
Fiber is received in the bale form as raw material for the spinning unit (one cotton bale weighing from 165 to 170 Kg). The bales are opened and teased out by the automatic Bale Opener. This also allows blending of bales of compatible quality for creating a Lot mixing which is both quality and cost effective. The opened fibber is then pneumatically fed into the Blow Room for cleaning of impurities in the fed cottons.
The fiber in the bale is carrying some foreign particles other than the prime usable fiber. Cleaning is required to remove these unwanted particles. Depending upon the quality of raw cotton and inherent trash content in it, the blow-room can remove 4-7% of impurities in the cottons fed to it. The Blow-room comprises of a set of cleaning machines which separate out the usable fibers from organic and other impurities. Fibers are also homogenized in blow-room and then conveyed to the Carding department for further cleaning and formation of a sliver or rope of even weight fiber which is the pre-process for starting the yarn formation.
The modern carding section is integrated to the blow-room and is the process where rest of the impurities in the fiber mix are removed and also linear density of fiber silver for making specific yarn counts is regulated. The blow-room to carding combination is expected to remove a total of 6 to 8% trash content form cotton fed into the blow-room. Carding is called as the Heart of spinning. “ well carded is half spun” is the sentence which is the basic of a spinning mill. The purpose of carding is individualization of fiber and cleaning the remaining micro dust, Nep (entangle fiber), making of cotton to sliver the first step to give a rounded form for producing yarn.
Object of Drawing is Parallelization of fiber, removing hooks created at blow room and carding stage& blending though doubling of sliver. The Finisher drawing called as Auto leveler drawing machine is the last passage of spinning yarn process for rectifying the even ness, blending of natural fibers through doubling of sliver and removing of hooks for improving length of fibers.
The function of Speed frame is to reduce the fine ness of sliver by drafting ( reduce weight per unit length) and imparting a little amount of twist for the next process called as Ring frame. It is the pre-form for the required Yarn count starts from the Roving department where the speed frame machines are used to impart marginal twist to the final finished/blended sliver. This helps in yarn formation in the next stage where yarn is formed with application of drafting and twist via the drafting and spindle system.
Ring Spinning or yarn Spinning is the core process in manufacturing of yarns. Ring spinning is done on a long frame machine (here each of 1200 spindles with auto-doffer unit) called Ring frame where the yarn is formed via combination of ring-spindle and roller drafting systems. The ring frames at the proposed Project are latest long frames, each with 1200 ring spindles, which are the individual production and delivery points for the yarn thus produced. The modern-day ring frames are high speed machines with spindle rpm of 18000 to 22500 rpm and also equipped with automatic doffing units and online process control to save on the manpower etc.
The net content of yarn on the ring frame delivery package (called Bobbin) varies from 50 to 60 gm/doff. It is thus essential to convert such bobbins into market usable package (called Cone) each cone weighing 1.8 to 2.5 Kg. This is done by processing small ring frame bobbins via Auto-coner machine which makes the large usable package; but more importantly it also `electronically` removes the yarn faults like irregular yarn density and others.
The yarn delivered from Auto-coner section is ready for packing and use. However, to stabilize and set the twist in the yarn, the auto-coner cones are further put into steam controlled chamber, i.e. Yarn conditioning machine, for about 1 hour for each batch for such twist setting which helps in further stabilizing the yarn.
The yarn package finished as above, is inspected in UV Light chamber for any foreign impurities like PP strands or others, and then packed into cartons of different market sizes. The cartons are moved out on pellets, into the warehouse and for dispatch to markets/buyers.
The yarn package finished as above, is inspected in UV Light chamber for any foreign impurities like PP strands or others, and then packed into cartons of different market sizes. The cartons are moved out on pellets, into the warehouse and for dispatch to markets/buyers. For export dispatches, the proposed Project has planned to ship on shrink-wrapped pellets (having 12-16 layers of the yarn cones), and where no cartons will be needed for such seaworthy packing .